从充换电服务到汽车生产,数字孪生技术在汽车行业应用有多广?
图片来源:视觉中国
数字孪生是映射现实物理世界的数字副本。通过集成人工智能、机器学习和传感器数据,建立一个可以实时更新的“真实”模型,用来支撑物理产品生命周期各项活动的决策。例如,蔚来能源云的智能选址系统,帮助推演换电站的布局地址,能够清晰知道新建站点在目前保有量下,换电站每天的单量、换电时间以及对周边换电站的影响等。
几天前的蔚来汽车NIO Power Day上,蔚来汽车高级副总裁沈斐首次对蔚来汽车充电换电网络的“大脑”——蔚来能源云的系统运作方式进行了详细披露。这套蔚来从2015年开始投入并自主研发的智能化体系,可以帮助蔚来布局充电换电网络,实时读取和远程监控设施的运营状况以及帮助用户规划智能出行路线。而数字孪生技术,是实现这些功能的核心基础。
此外,蔚来汽车的充电桩、换电站、电池以及蔚来车都以数字形式储存在蔚来能源云中。沈斐介绍,通过蔚来能源云的智能运维系统,工作人员能准确了解换电站储备的电池数量、电池衰减程度、运行健康状况、用户全程换电时长等,并基于数据分析情况判断做出决策。
“通过数字化空间建立一座换电站的模型后,可以直观看到电池仓内的换电整个过程,甚至精细到一个螺栓是否拧紧。”沈斐说,“我们已经有近100个换电站处于无人值守的自助换电运行状态,调度运营中心远程通过数字空间,了解换电站发生的一切,一旦某个部件发生故障,就可以准确定位到并加以解决。”
事实上,数字孪生技术并不局限于充换电服务,它已经在汽车行业得到广泛应用,包括汽车及零部件的研发、汽车生产以及供应链管理等多个环节,尤其在汽车生产的智能制造领域,是汽车公司布局的重点。
特斯拉是数字孪生技术产业化应用的试水者。2011年,特斯拉成立设计工作室(Design Studio),赋予其超级工厂数字孪生能力。针对汽车制造特点,特斯拉对美国航天局的数字孪生技术“降维”使用,降低仿真精度要求,为每一辆出厂的汽车都配备了数字孪生模型,并根据物联网传感器接收到的数据,对汽车程序进行实时更新,为用户提供持续优化。
在汽车生产制造方面,以上汽通用奥特能超级工厂为例,奥特能超级工厂电池生产的涂胶、合盖等工艺,由基于数字孪生技术的机器人自动完成。设备加工方案在设计初期,会针对轨迹、速度、出胶量等工艺参数进行数百次虚拟仿真,生产时将仿真运行后的最优程序输出到现场设备,并配合3D视觉手段,全系统实现测量精度小于0.1mm。
宝马将数字孪生技术应用到物流环节支持车辆的准时交付。通过堆场管理系统,将实时物流数据与3D模型相结合,模拟各种物流场景,实现对集装箱的精确管理。并且,工作人员能随时了解堆场内发生情况,更高效地为汽车生产提供零部件。
值得一提的是,宝马投资了150亿在沈阳建成的里达工厂是一座从最开始就完全在虚拟环境进行规划和模拟的工厂。根据宝马官方介绍,厂区规划、建筑设计、生产线布局以及设备调试均在Epic Games虚幻引擎3D创作平台创建数字孪生模型并进行模拟。
通过虚拟世界和现实世界的融合,工厂各部门可以提前发现设计和系统运行中存在的问题与有待改进之处,并及时进行调整与优化,后续建设执行环节中的返工次数得到了大幅减少。里达工厂从动工到投产仅用了两年多时间,比正常工期缩短6个月。
国内汽车公司同样在数字孪生技术的应用上不遗余力。一汽集团基于数字孪生的协同设计和虚拟仿真平台,将产品开发周期缩减6个月以上;基于5G+工业互联网的数字化工厂,应用物联网、数字孪生、混合现实等技术,实现冲压、焊装、涂装、总装四大工艺智能化生产,整车生准周期压缩7个月,订单交付周期缩短26%以上。
长安汽车则在去年发布了基于“用户-车企-开发者”的全链路打通的全场景数字孪生开发开放平台。长安汽车董事长朱荣华介绍,该平台是国内首次实现驾驶、座舱、车控三域打通的整车级虚拟仿真环境,实现全车功能场景可编排。
数字化服务提供商埃森哲大中华区产品制造事业部董事总经理蔡沈隽告诉界面新闻,数字孪生在国内汽车公司之间正在逐步推广应用,生产车间高度自动化已经变成可能。
“生产车间产线上发生的每一件事情,都在虚拟的数字环境里实时可见,以往不能及时注意到的问题,能够基于数据方式进行主动预警和干预,既提高了企业生产韧性,又降低了企业生产成本。”
随着汽车行业“新四化”变革的进程,数字孪生正在以前所未有的速度应用于汽车及零部件企业。蔡沈隽认为,汽车公司需要思考如何加速包括生产制造在内的大供应链数字化转型和提升,迎接未来的挑战。
声明:本网转发此文章,旨在为读者提供更多信息资讯,所涉内容不构成投资、消费建议。文章事实如有疑问,请与有关方核实,文章观点非本网观点,仅供读者参考。
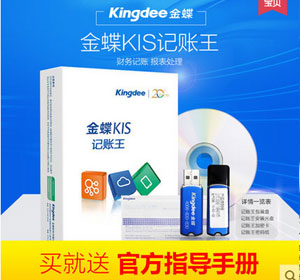